5 key advantages of using PLC systems in manufacturing
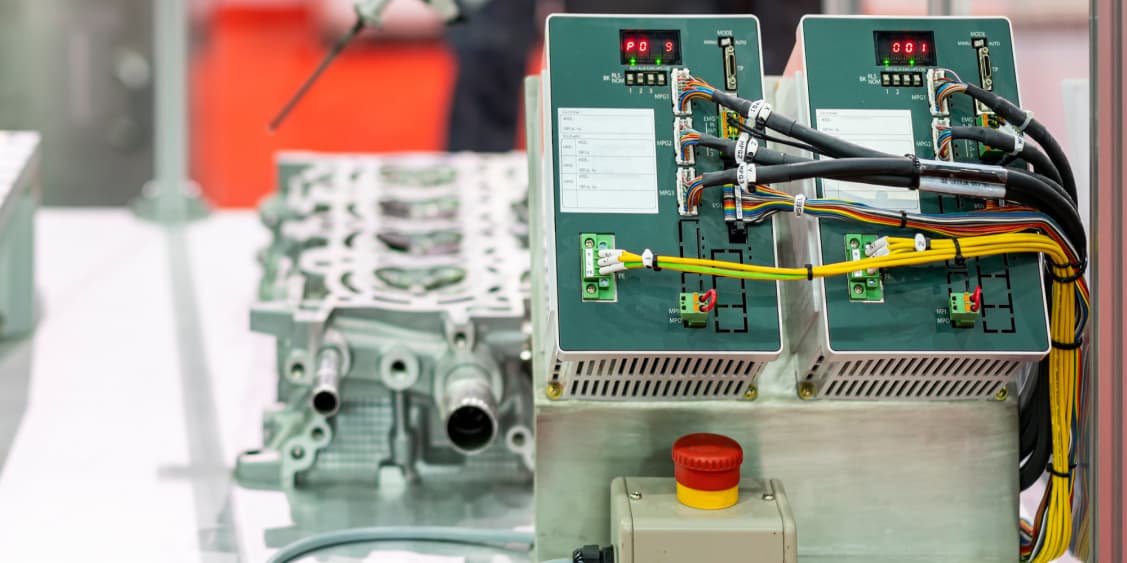
We supply a wide range of PLCs here at LED Controls, built to the very highest standards by global manufacturers, including IMO and ABB. PLCs, or Programmable Logic Controllers, are essentially small industrial computers, which are designed to control a variety of processes in heavy-duty commercial environments, and other industrial settings. They’re widely used by countless national businesses and international corporations, largely because of the potent range of benefits they provide. This week, we’ve rounded up some of the biggest.
Better performance and precision in a more compact package
PLCs rely on advanced computational methods to offer a robust means of complex control for your systems, and they’re capable of acting on inputs from a diverse array of devices and sensors in the modern industrial setting. What’s more, due to their solid state components, they can respond to these inputs a lot faster than traditional relay systems, and react equally quickly.
These faster processing speeds allows them to achieve more advanced control over more complex systems than older relay-and-timer systems, which makes PLCs particularly well-suited to applications that involve process automation and robotics. As an extra bonus, the solid state element of their design generally means they’re more physically compact than older systems, which can further increase operational efficiency.
Remote access capabilities and increased safety
One of the most useful characteristics of PLCs for many companies is that their digital nature and networking capabilities allow for the system to be monitored remotely, providing detailed information on its performance (or condition monitoring data) to a central control location. That control location may be on-site, or it may be hundreds of miles away – effectively, enabling you to maximise a system’s performance without necessarily needing a human presence to do so.
In situations where a staff member’s presence is indeed required on-site, PLCs can be used to control the displays mounted to the control panel, which provides a useful central interface to de-bug, monitor and optimise performance in-situ. What’s more, PLCs can also be programmed to perform safety functions like emergency shutdowns and machine guarding, enhancing safety for any staff on-site.
More cost-effective and economical
PLCs technically have a higher initial outlay than older relay and timer systems, but they require less maintenance and have a longer operational lifespan, making them the more economical option in the long run.
What’s more, their digital nature means that they only have to be programmed once, and then they can be rolled out across multiple versions of the same system. They can save you time and costs by freeing you from the need to write the same program multiple times – once you have the physical assets for the new system, you can deploy it promptly, maximising productivity and saving you on setup costs.
Flexible and scalable
PLCs can be programmed to perform a wide range of tasks, from simple on/off control to more complex motion control. That makes them inherently versatile, and since they’re a software-based solution, that gives them greater flexibility to adapt to the development of any relevant systems or operations. It also helps that PLCs have a highly modular design which can be easily expanded by adding more modules or controllers, further enhancing their scalability.
Plus, the remote access capabilities we touched on above also means that software updates can be typically implemented remotely, including any necessary debugging.
Reliable and easy to maintain
PLCs use solid state components, which allows them to run more reliably with less degradation over time. What’s more, their modular design means that faulty components can be easily replaced without affecting the rest of the system, and they have built-in diagnostic options that make troubleshooting simpler and more straightforward, too. The data logging capabilities of PLCs also mean they can record data on machine performance, which can be used on an ongoing basis for troubleshooting and predictive maintenance – helping to reduce downtime and improve overall efficiency.
Those are just a couple of the major universal benefits associated with PLCs – you may be able to enjoy a range of further one specific to your business! And if you’re in the market to buy the best quality Programmable Logic Controllers at the very best prices, that’s exactly where we can help here at LED Controls. With decades of experience behind us, we supply a wide range of PLCs from global manufacturers, including IMO and ABB. Feel free to look at what we’ve got available, and if you have any questions or need any advice, you can always give us a call on 01706 242050. We’re here to help!