We use cookies to make your experience better. To comply with the new e-Privacy directive, we need to ask for your consent to set the cookies. Learn more.
5 key operational pieces of equipment to review in the New Year
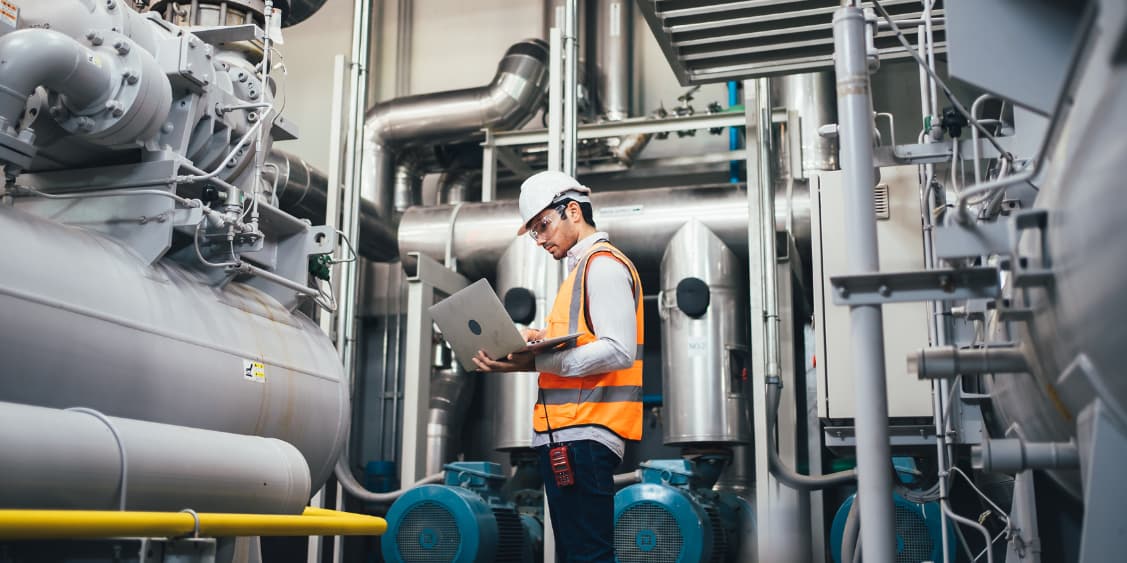
We’re now officially into the start of a brand new year, which makes it an ideal time to assess the state of operations-critical equipment. Almost all components in factory automation are specifically designed for durability and reliability – but they can all still benefit from regular maintenance, and prompt replacement at the end of their operational lifespan. Here are our top recommendations as to which components it’s best to look at first.
Programmable logic controllers
Programmable logic controllers should generally be reviewed annually, or as dictated by the manufacturer’s guidance, particularly in high-demand environments. Otherwise, they can be prone to software glitches, communication failures, or total breakdowns during production runs – which can obviously have massive consequences. A single malfunctioning controller can halt operations or lead to expensive troubleshooting, causing avoidable (and very costly) downtime.
Regular maintenance should typically include inspecting I/O modules, updating firmware, and testing system responsiveness to pre-empt any potential for disruption.
Switchgear and monitoring systems
Switchgear systems typically require maintenance intervals of three to five years, though high-usage environments may demand shorter cycles. Typical consequences of unchecked wear and tear can lead to overheating, blown fuses, or even electrical fires. Monitoring systems also degrade over time, potentially failing to detect issues that could compromise safety.
To counter those risks, routine inspections should focus on verifying insulation integrity, recalibrating monitoring devices, and replacing worn-out components. As well as helping to minimise the risk of expensive failures, it can also help to extend the life of your overall electrical infrastructure as a whole.
Enclosures and climate control
Enclosures and climate control equipment require more frequent checking – ideally quarterly to annual inspections (depending on the environmental conditions they are exposed to). Otherwise, they can suffer from overheating, corrosion, or contamination of the sensitive equipment they protect.
Dust accumulation, clogged cooling units, or damaged seals can render enclosures ineffective. Regular checks for air filters, temperature regulation, and physical damage are essential to keep internal components safe. If you’re pressed for time, a once-over can be enough for the short-term, but generally it’s best to make the time to do a more detailed inspection when you can.
Terminals and connectors
Terminals and connectors may seem low-maintenance, but quarterly inspections are vital to ensure secure and reliable connections. Loose or corroded terminals can cause voltage drops, electrical arcing, or intermittent failures that ripple through your entire system.
Left unchecked, a minor issue with connectors can escalate into significant downtime as technicians scramble to diagnose the root cause. Proper tightening, cleaning, and replacement of worn components are simple steps, but they’re hugely effective for maintaining smooth operations.
Sensors and machine safety systems
Sensors and safety systems require thorough checks every six months to a year, depending on usage. If neglected, drifting sensors may provide inaccurate data, while malfunctioning safety interlocks could even result in faulty inputs or emergency shutdowns. That can result in fines for non-compliance – not to mention putting staff at risk. Preventative maintenance should include recalibration, functionality testing, and ensuring all safety devices meet the latest regulatory standards.
Those are all our suggestions in a nutshell! And of course, if you ever need any replacements or new components to help scale up your operations in 2025, that’s exactly where we can help here at LED Controls. We supply a wide range of components, including Programmable Logic Controllers, variable speed drives, and Motor Control Gear equipment – many sourced from globally-renowned manufacturers, including IMO and ABB. Feel free to look at what we’ve got available, and if you have any questions or need any advice, you can always give us a call on 01706 242050. We’re here to help!